MHE Equipment Categories – Types of Material Handling Equipment
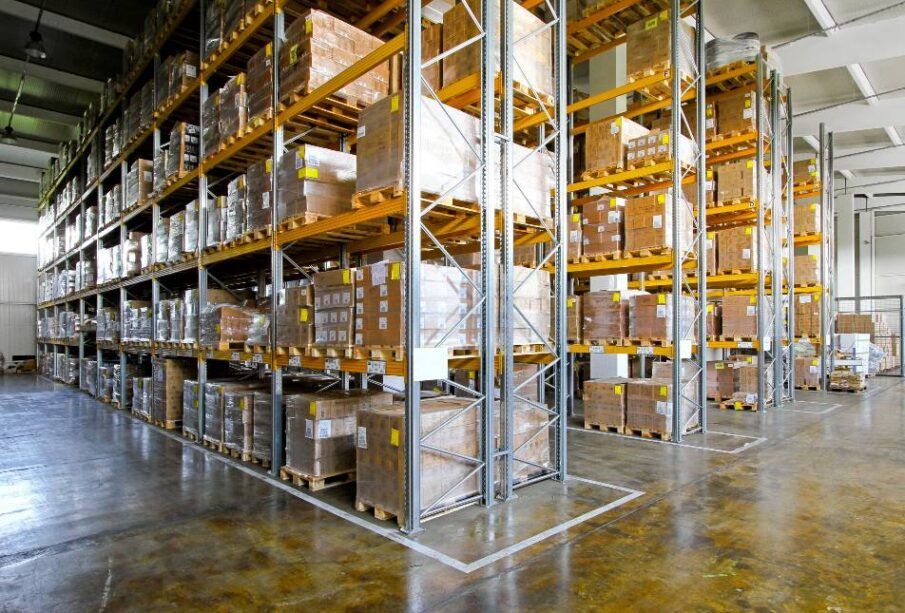
Broadly there are Four Types of Material Handling Equipment: storage and retrieval, engineered systems, industrial trucks, and bulk material handlers. Storage equipment—pallet racks, shelving, mezzanines—helps maximize vertical cube utilization and organizes where SKUs are placed for quick access. These are automated conveyors, sortation lines, carousels, pallet shuttles and AS/RS solutions that have been engineered for high-volume, low-labour throughput applications. Industrial trucks include both manual and powered vehicles—hand trucks, order pickers, counterbalanced forklifts, reach trucks—that transport loads between dock, floor, and rack.
Bulk material handling involves all the equipment like warehouse trolleys that transport granulated or free-flowing items like grain, ores, or chemicals like conveyors, hoppers, and stackers. Every category has its own unique purpose but the majority of the tasks fall to a combination of the two. The beauty of the choice is knowing what combination fits your unique operating profile—how quickly does stuff have to move, how tightly packed does it need to be held and how irregular is the demand profile? Thinking about these categories helps you to create a toolbox rather than a crutch.
Nature of the Material
Wherein the product itself dictates its proper movement and stow through things like size, weight, fragility, temperature sensitivity as well as how it is packaged. For example, wide-fork attachments and custom clamps may be needed for bulky items, while those that contain delicate electronics would require cushioned racks and low-vibration conveyors. These subtleties are preventing damage, rejects or re-work on demand later — and cost.
Throughput and Volume
The varying peaks and average levels of demand determine how much capacity is needed. So a 3,000-parcel-an-hour conveyor may look good on paper but will struggle when holiday surges push volume up to 5,000 and the sortation chutes start to choke. By modelling your throughput profiles you can then size your equipment properly, avoiding the risk of having it idle wastefully during slow seasons or creating a bottleneck during spikes.
Facility configuration and constraints of space
Physical constraints on the size of equipment footprints, turning radii, are largely a function of square footage, column spacing, ceiling height, and dock door positions. For instance, very narrow aisle (VNA) lift trucks fit into aisles as narrow as five feet, but this design sacrifices operator visibility and battery life. Early constraints help you reach for equipment that fits the building instead of fighting with it via detailed surveys and CAD drawings.
Operational Environment
If you ignore it, temperature extremes, humidity, dust, and polluted chemicals will shorten the service life of the equipment. Cold-storage forklifts have sealed bearings and heaters to keep hydraulic oil from thickening outdoors yard carriers have weatherproof cabins and extra clearance. Adapting materials, seals and coatings to the environment enhances uptime and minimizes maintenance expenses.
Ergonomics and Worker Safety
Despite of automation, Material handling still is a labour-intensive task. Doing the same motion over and over like reaching or twisting or picking some item or equipment up causes injuries and as a results loss in productivity. Lifting equipment that raises products to waist level—lift tables, pick-to-light modules, powered pallet jacks—minimizes strain. Which features like proximity sensors and speed governors mitigate the dangers of collision? Paying for ergonomic design increases efficiency and reduces workers comp claims and morale-sapping downtime.
Industry(s) of the Future & Net Zero
No longer relegated to the fringe, electric vehicles, regenerative braking, and high-efficiency motors offer real savings as energy costs rise and ESG reports become common. Hidden operating costs are uncovered and sustainability goals can be achieved without sacrificing performance when using life-cycle energy consumption (not just purchase price) as the means to evaluate equipment selection.
Final thoughts
Equipment from equip2go that can exchange data has become an essential element for warehouse management systems, ERP interfaces, and IoT sensors. Real-time tracking of where a crate is, whether the battery is charged, or maintenance codes via barcode scanners, RFID readers, and on-board telematics. If you use equipment that has open APIs or standard communication protocols, that will simplify integration now and make you better able to implement advanced analytics and predictive maintenance in the future.